Are your manufacturers treating workers fairly, compensating them enough, and prioritizing their health and safety? Do you have clear visibility into their practices, and are you taking steps to ensure they are in line with all labor laws?
Social compliance is a significant concern for many companies today. It is the process of protecting the rights, health, and safety of employees and workers in the supply and distribution chain. Social compliance involves monitoring suppliers to ensure their employment practices are legal and ethical and they are taking steps to address any issues.
Here we talk about how social compliance works and how to audit a manufacturer to ensure your supply chain is free of social compliance issues.
Why Should You Care About Social Compliance?
Imagine that, unbeknownst to you, one of your manufacturers uses child labor to make your products. Word gets out, and suddenly you’re in the media’s crosshairs as they report the news.
Now your company is caught up in a controversy over something you had no idea was going on. Your brand reputation gets dragged through the mud, and all you can do is sit there biting your nails and waiting for the sales numbers to drop.
Concerns about your brand reputation aside, wouldn’t it be better to feel confident that your supply chain is free of workers’ rights violations? Don’t you want to have a pulse on how your suppliers operate and be able to make improvements if any issues arise?
Developing a social compliance program helps you to accomplish this, and audits play an essential role.
What is a Social Compliance Audit?
A social compliance audit is a factory assessment that aims to uncover issues related to employment laws and ethical concerns. It involves sending an auditor to the manufacturing facility for a first-hand look at its operations.
It typically involves observing the factory, reviewing work records, and interviewing workers and management. The goal is to uncover hidden issues like child labor, forced labor, unfair disciplinary practices, or safety concerns.
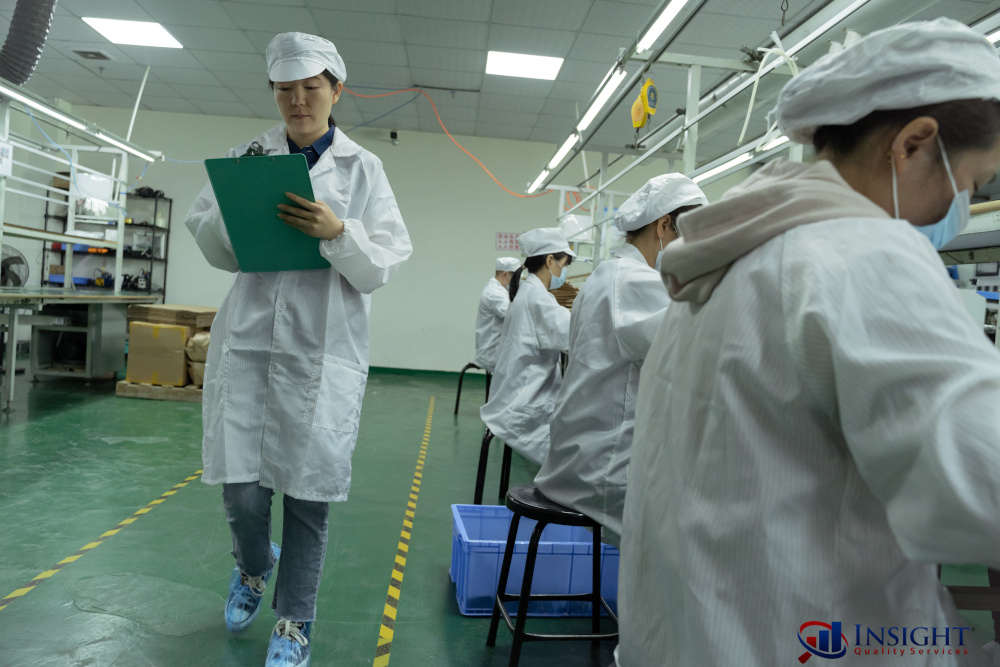
Some big retailers require their vendors to conduct social audits to ensure good practices. And brands focusing on corporate social responsibility (CSR) tend to have well-developed auditing programs.
The SA8000 Standard from SAI is one of the most well-regarded standards for conducting these audits.
How to Audit Using the SA8000 Standard (9 Areas Covered)
An SA8000 audit is conducted based on the SA8000 standard, considered “the world’s leading social certification program.” It aims to help organizations “conduct business in a way that is fair and decent for workers and to demonstrate their adherence to the highest social standards.”
SA8000 is sometimes used for certification but is also used as a standard to hold suppliers to.
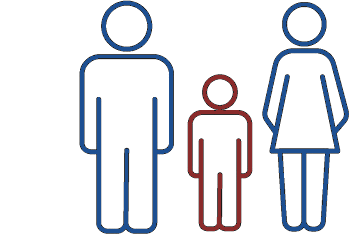
#1 Child Labor
The auditor verifies that all workers are above the age of 16 or the legal working age in the area. They assess the company’s hiring practices, such as identity verification, to ensure no underage workers are mistakenly hired. They also verify that working conditions for employees under 18 are suitable and in accordance with local laws.
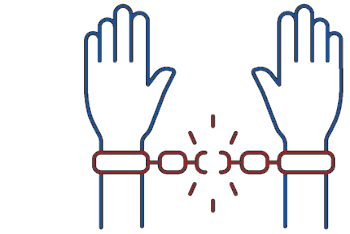
#2 Forced or Compulsory Labor
The auditor looks for evidence that the company never holds documents like ID cards or passports, with workers unable to retrieve them. They check to verify that the facility does not withhold wages, allows freedom of movement, and is free from prisoner employment.
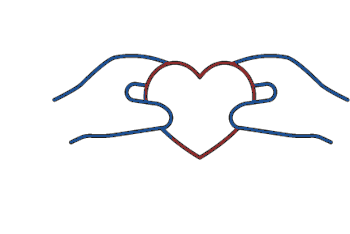
#3 Health and Safety
The auditor looks for documentation of compliance with building safety requirements. They verify whether the facility has non-expired fire safety documentation, is operating in a building that matches its intended purpose, and has documentation of safety inspections for the building and machines.
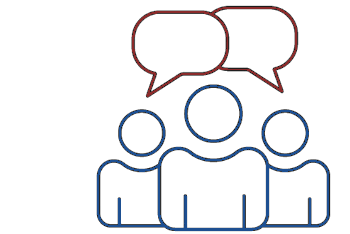
#4 Freedom of Association
The auditor verifies that the employer respects all personnel’s right to bargain collectively or, where collective bargaining is restricted, have access to alternate means. They look for evidence that employees can meet with management to air grievances.
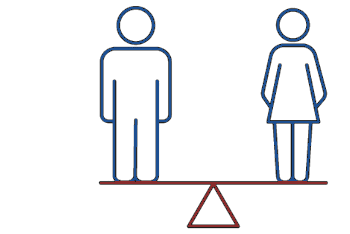
#5 Discrimination
The auditor reviews employer practices related to hiring, compensation, access to training, promotion, termination, or retirement. They look for evidence that employees are receiving equal pay for equal work when considering their experience and seniority.
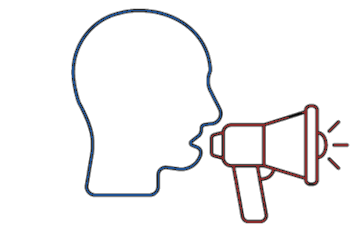
#6 Disciplinary Practices
The auditor looks for evidence that employees at the facility are free from harassment and mental, physical, and verbal abuse. They determine whether disciplinary measures implemented by the facility are fully in line with the law and are not excessive.
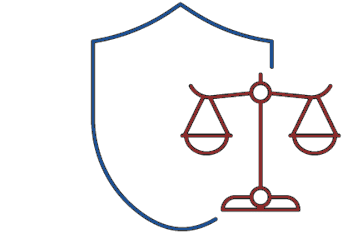
#7 Working Hours
The auditor checks to see if employees are working regular and overtime hours in accordance with the law and receiving appropriate rest breaks. The audit seeks to verify that the employee is also getting an appropriate amount of time off.
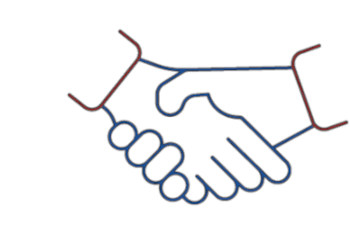
#8 Remuneration
The auditor investigates whether workers are being paid fairly and receiving adequate wages. They look for evidence that the time and frequency of payment are in accordance with the law, employees are paid during their probation periods, and any required overtime is paid.
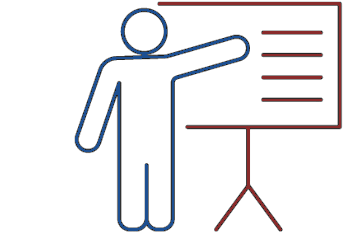
#9 Management System
The auditor reviews the company’s management system to ensure that policies are in place for social accountability. They also investigate whether the manufacturer monitors the practices of any subcontractors they work with.
Social Compliance Helps Ensure an Ethical Supply Chain
Social compliance is essential for companies that care about the treatment of workers in their supply chain and want to avoid working with unethical manufacturers. Auditing plays a vital role in any social compliance program, and the SA8000 standard is a helpful guide for these assessments.
If you want to ensure that your supply chain is free of ethical issues, consider conducting an audit with experienced in-house staff or through a reliable service provider.
This article was originally published on the Insight Quality Services website.
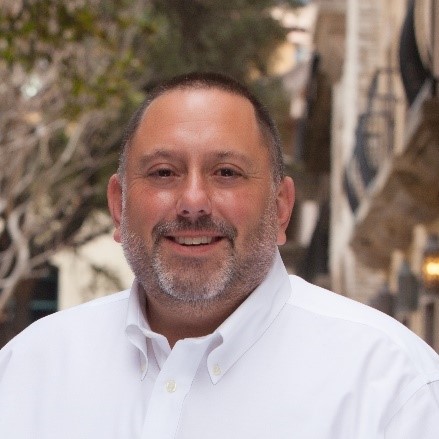
Andy Church – Founder & CEO of Insight Quality Services
Andy Church has over 20 years of experience in product quality and founded his company in 2014. Insight Quality provides product inspections, factory audits, lab testing, and other services in 17 countries worldwide.
Source quality and socially-complied products on our e-Marketplace by clicking below banners:
Subscribe to NewsBites and stay updated on the latest business trends and news.
Related posts:
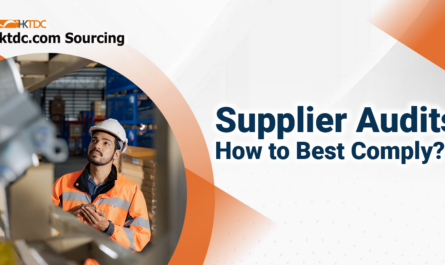
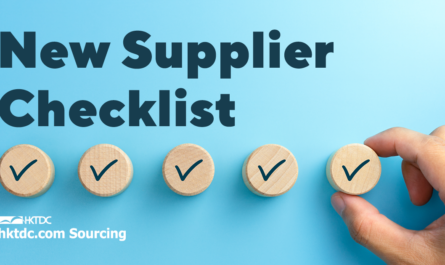
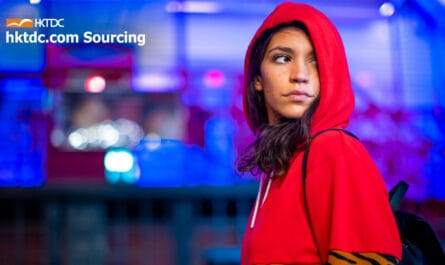
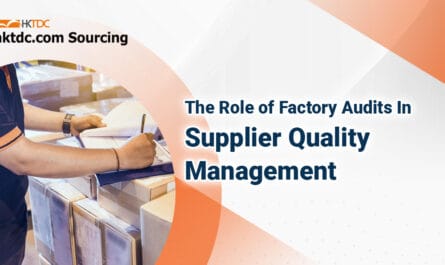